News Releases February 08, 2021
Remote maintenance capability boosts North Canterbury farm contracting business
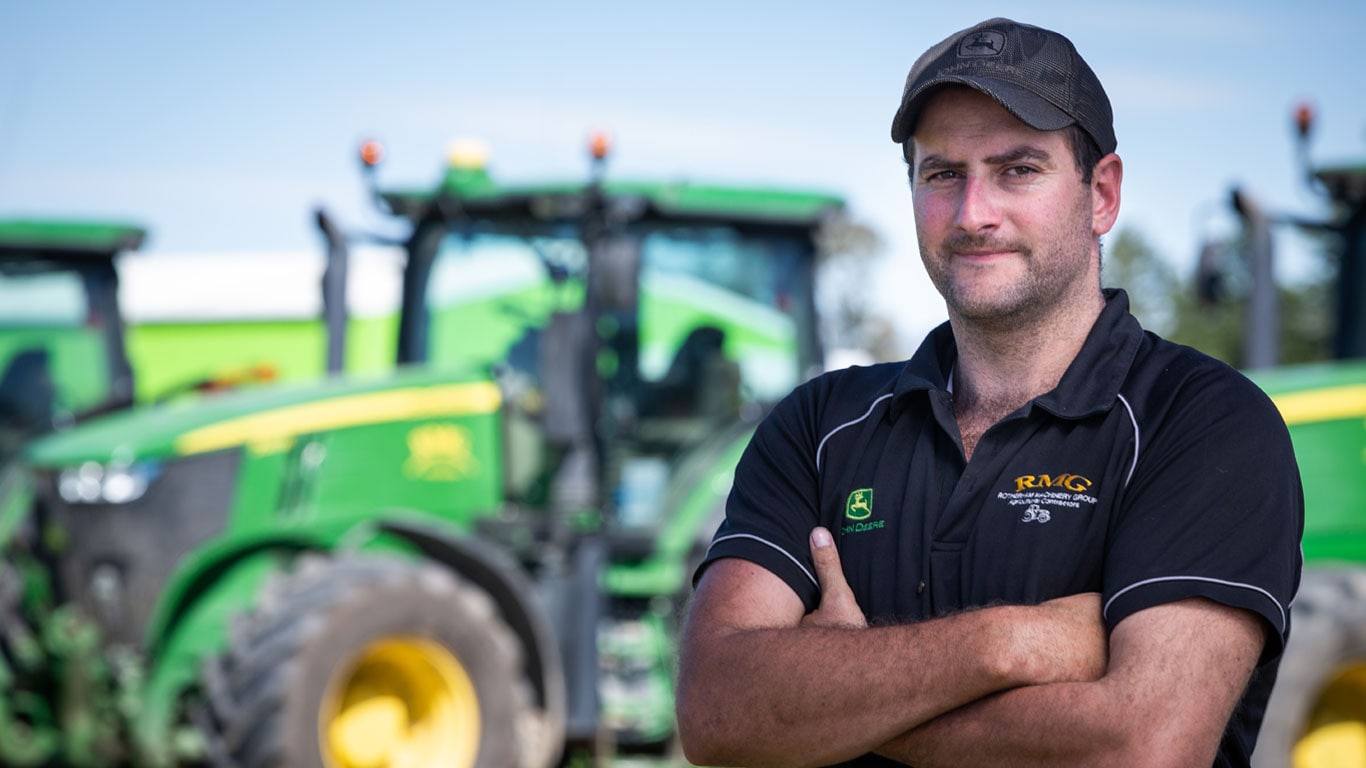
Rotherham Machinery Group, Manager, John Ranford is given peace of mind his fleet of machinery is running at full capacity through John Deere Connected Support.
Crestmead, Queensland (08 February, 2021) — A DIVERSE customer base of dairy, beef, sheep and cropping enterprises scattered throughout the North Canterbury Plains means the reliability of the equipment used by farming contractor Rotherham Machinery Group (RMG) underpins the success of the business.
Established by three farmers more than 25 years ago, first as a syndicate to expand the equipment lineup across their own sheep and beef operations, RMG now services 20 farms in the region, to which timely and consistent on-farm work must be provided.
RMG Manager, John Ranford, said the breadth and diversity of the customer portfolio meant he needed peace of mind that the machinery fleet worked to full capacity at all times, which is what drew him to embrace John Deere Connected Support™.
"There are a lot of moving parts to this business, so it's essential each of the elements are operating smoothly," John said.
Connected Support, a suite of digital tools intrinsically linking farmers and contractors with their dealership, underwrites efficient operations by allowing John Deere technicians to monitor machinery performance and remotely provide vital back-up support.
In John's case, the industry-leading tech means his local dealer, Drummond & Etheridge, Rolleston, can deliver integrated support to RMG's John Deere 750A six-metre direct drill, a 6155M and three full-spec John Deere 7210Rs.
"Given we are based about an hour-and-a-half away from our local dealer, it's much more efficient for them to be able to see how the machine is running remotely and take action straight away," John said.
"It also allows them to preempt issues and provide proactive solutions, which saves a lot of time."
TIME OF THE ESSENCE
Based near Culverden, about 100 km outside of Christchurch, RMG homes in on the productive farming basin that is bordered by the Hurunui and Waiau rivers.
"The season comes to a peak for us in spring when there is the overlap between drilling for specialist seeds for winter crops, and silage and baling are in full swing," John said.
Throughout the rest of the year, services provided by RMG include fertilising, spraying, land clearing and development, mowing, mulching and ploughing.
Service ADVISOR Remote™, Connected Support's online tool to allow technicians to analyse machine information instantly from any location, has proved invaluable.
"This is a feature we have found extremely handy," John said.
"In the past, if we had a problem the mechanic would have to come all the way out to the farm to diagnose it.
"It's much more efficient for them to be able to see how the machine is running, look at the trouble codes, and bring the correct parts and tools for the job if they do need to come out."
ENSURING RELIABILITY
To John, one of the best indicators the business is performing comes in the knowledge the fleet is operating at full steam, and he can quickly gauge how things are tracking when he looks across the RMG equipment yard.
"When the yard is empty here, I know all our machinery is out on farms and running at 100%," he said.
"That indicates we are getting through a lot of work and our clients are happy."
John opts for John Deere equipment due to its reliability and it also comes with the knowledge unexpected issues are avoided through the use of John Deere Expert Alerts™. Expert Alerts is a Connected Support tool that proactively notifies dealers of any potential machine issues that can occur in the throes of everyday farming before it becomes symptomatic, maximising uptime.
His dealer can also actively monitor machine Diagnostic Trouble Codes (DTCs) to determine the best resolution to keep his machines at optimal capacity.
"I have had phone calls from the technician at the dealership as a result of proactively monitoring trouble codes," John said.
"For example, once a new staff member was operating a tractor and our technician called to let me know the machine was getting close to overheating. I was able to immediately address the situation to ensure it didn't happen again."
On another occasion, John and his team were surprised to receive a phone call when they were discing on a hilly slope — it was their John Deere dealer, ringing to advise them to check the oil in the tractor they were using.
"We quickly realised it was because the machine was on such a slant the oil had dropped past the sensor," he said.
"It gave us a bit of a laugh at the time, but also highlighted how swiftly our dealer could respond if we faced a real problem."
EMPOWERED TEAMWORK
Rotherham Machinery Group has four full-time staff and brings in three sub-contractors to run trucks for silage and baling work during the peak season.
"I am quite lucky that I get a lot of repeat staff," he said.
"However, for new or contract employees training can be a challenge every year, but it's becoming less so with the ease of use of modern machinery."
John Deere AutoTrac™ steering has proven invaluable in simplifying this training while increasing work quality by ensuring consistency, no matter who is behind the wheel. It has also contributed significantly to operator comfort.
AutoTrac enables hands-free steering of equipment by using GPS coordinates to control the tractor. The high precision assisted steering system means operators can focus more on the task at hand, and the implements in the ground.
"This feature has taken the fatigue away from driving which increases the quality of the job," John said.
Using John Deere Operations Center mobile app, also means John can stay informed of where his operators are when he is not with them in the paddock.
"The location of the machines also assists regular maintenance work too as it coordinates with Connected Support," he said.
"If a technician happens to be in the area they can log in and see where all the equipment is parked, and if there's any maintenance required on equipment nearby they can duck straight out to that machine."
John is still hands-on in the business and spends much of his time working with farmers while contracts are successfully being rolled out.
"The most rewarding part of the job, for me, is when it's all running smoothly. Technology and reliable equipment help guarantee that efficiency and consistency for us."
About John Deere:
Deere & Company (NYSE: DE) is a world leader in providing advanced products and services and is committed to the success of customers whose work is linked to the land - those who cultivate, harvest, transform, enrich and build upon the land to meet the world's dramatically increasing need for food, fuel, shelter and infrastructure. Since 1837, John Deere has delivered innovative products of superior quality built on a tradition of integrity. For more information, visit John Deere at its worldwide website at JohnDeere.com in New Zealand at JohnDeere.co.nz.
Media Contacts:
Stacey Wordsworth
0438 394 371
stacey.wordsworth@bluehillpr.com.au
Hannah Hardy
0421 196 004
hannah.hardy@bluehillpr.com.au