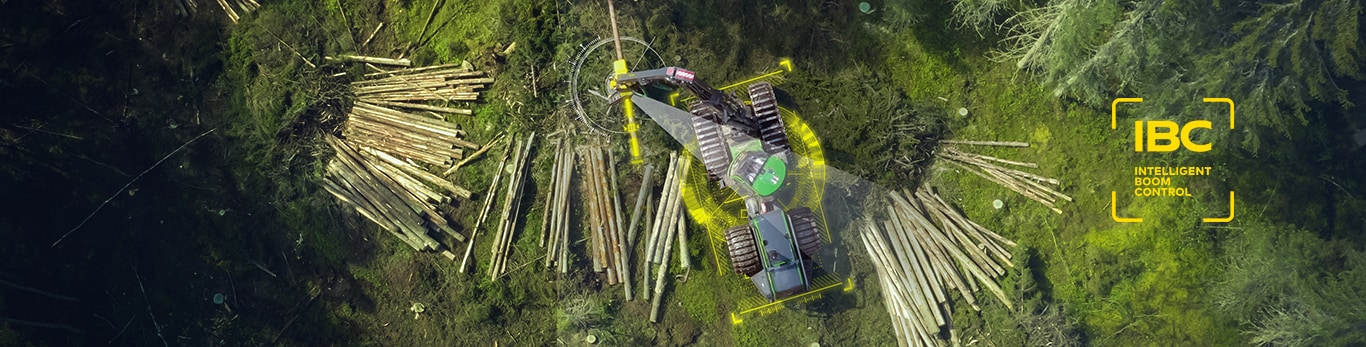
John Deere introduced Intelligent Boom Control (IBC) for forwarders in 2013. With IBC, boom control is precise, fast and easy because the operator can focus on controlling the grapple rather than the boom joint movements. IBC was also introduced for harvesters in 2017. In the harvester, IBC has been adjusted to the work cycle; the trajectory and functioning of the boom adjust automatically to the harvester's work phases.
Operator takes the harvester head to the desired place. Sensors recognize the location of the head and the system adjusts boom movements and extension automatically. The operation of IBC in harvesters has been adapted to harvester’s work cycle.
The harvesters 1270H, with harvester head H425 and H424, and 1470H, with harvester head H425, are available with harvester head over-rotation prevention when equipped with the IBC 3.0 and the rotating and levelling cabin. This combination offers even more features that assist the machine operators in their work. Feeding assistant helps avoid feeding towards the cabin and helps the operator find safe ways of working that keep the machine intact. This is possible because the IBC registers the log's orientation. Sawing assistant helps avoid sawing towards the cabin. These new features, while assisting the operators in their work, improve machine uptime and help to keep the machine in good condition.
Intelligent Boom Control is taking the use of harvesters to a completely new level. With the harvester’s IBC, the operator controls only the harvester head while the system takes care of the boom’s movement.
Operators can adjust the overall speed of the IBC system to accommodate their needs. They can also adjust the speed between various boom parts or change it by manually using the extension boom during operation. Switching between IBC and conventional boom control is done with a press of a button.
With IBC, the boom is very precise and easy to operate: the operator controls the boom tip directly instead of controlling independent boom joint movements. Left mini lever controls the horizontal movement of the grapple.
The right mini lever controls the vertical movement of the grapple.
The IBC system features electrical end damping for all the main boom movement directions. The system dampens the cylinder end movements softly and stops strong blow-like loads in the end positions.
With just the push of a button, the boom automatically returns to the load space. Additionally, the boom can be folded into transport position and unfolded back to the working mode at the push of a button.
IBC 3.0 is standard in the large H Series forwarders.
The system dampens the cylinder end movements softly and stops strong blow-like loads in the end positions, making for smoother operation and also improving the boom’s durability.
IBC controls intelligently the use of extension in different stages, which makes work much easier giving the operator more time to plan the next move. The boom is very accurate and steady even with longest reaches and new operators find it easy to learn the work.
The end damping stops the blow-like loads of the cylinder ends and the operator does not need to watch for boom positions. Work is more fluent and the boom structures and hydraulic cylinders last longer.
When the harvester head is driven to the tree, it moves automatically to the cutting height. After the cutting, when the boom is drawn in, the harvester head moves automatically to the processing height.
The boom tip automatically follows the desired trajectory. The slope mode adjusts the trajectory for working on a slope.
With the optional IBC, operators no longer need to control each independent boom function separately. One joystick moves the boom tip horizontally, while a second guides it vertically, and IBC automatically guides the boom and cylinders accordingly. IBC also automatically controls swing speed based on the overall position of the attachment.
IBC is easily configurable to user preference, so operators can adapt their motions to the application. Individual user settings can be saved in up to eight separate profiles, to accommodate multiple skill and experience levels.